Our Process
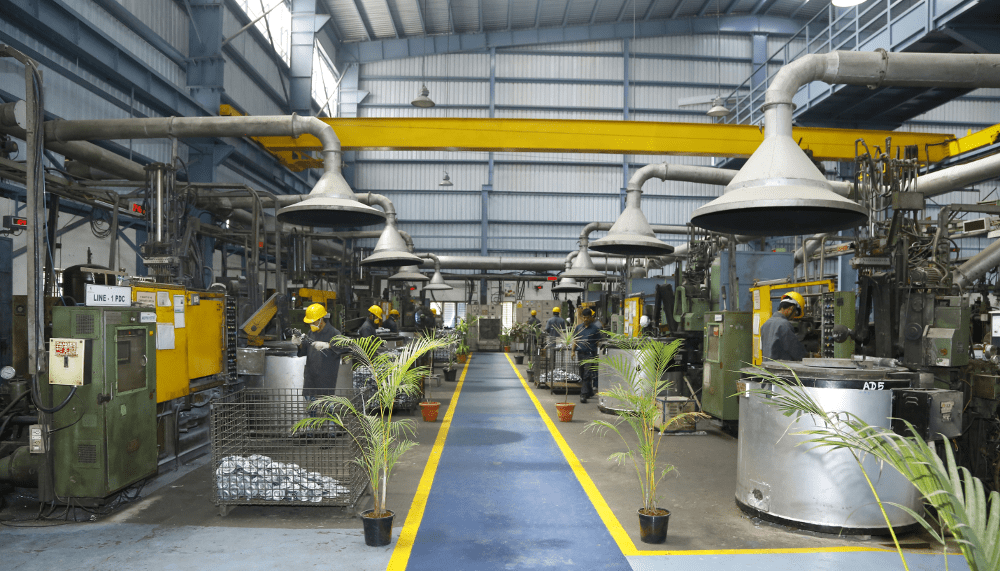
Introduction to Die-casting
Die casting in itself is a unique process. Since the technology consists of mechanical, electrical, electronics, thermodynamics, hydraulics, and metallurgy, the success of die casting purely depends on process control. The soundness of casting depends on how the process is controlled during die casting.
Alubee is having its state-of-the-art Die Casting facility equipped with a range of machines starting from 125 tons, 250 tons, and up to 350 tons capacity. Also, the progressive plan is to add higher tonnage machines to cater to a wide range of customers and varieties of products.
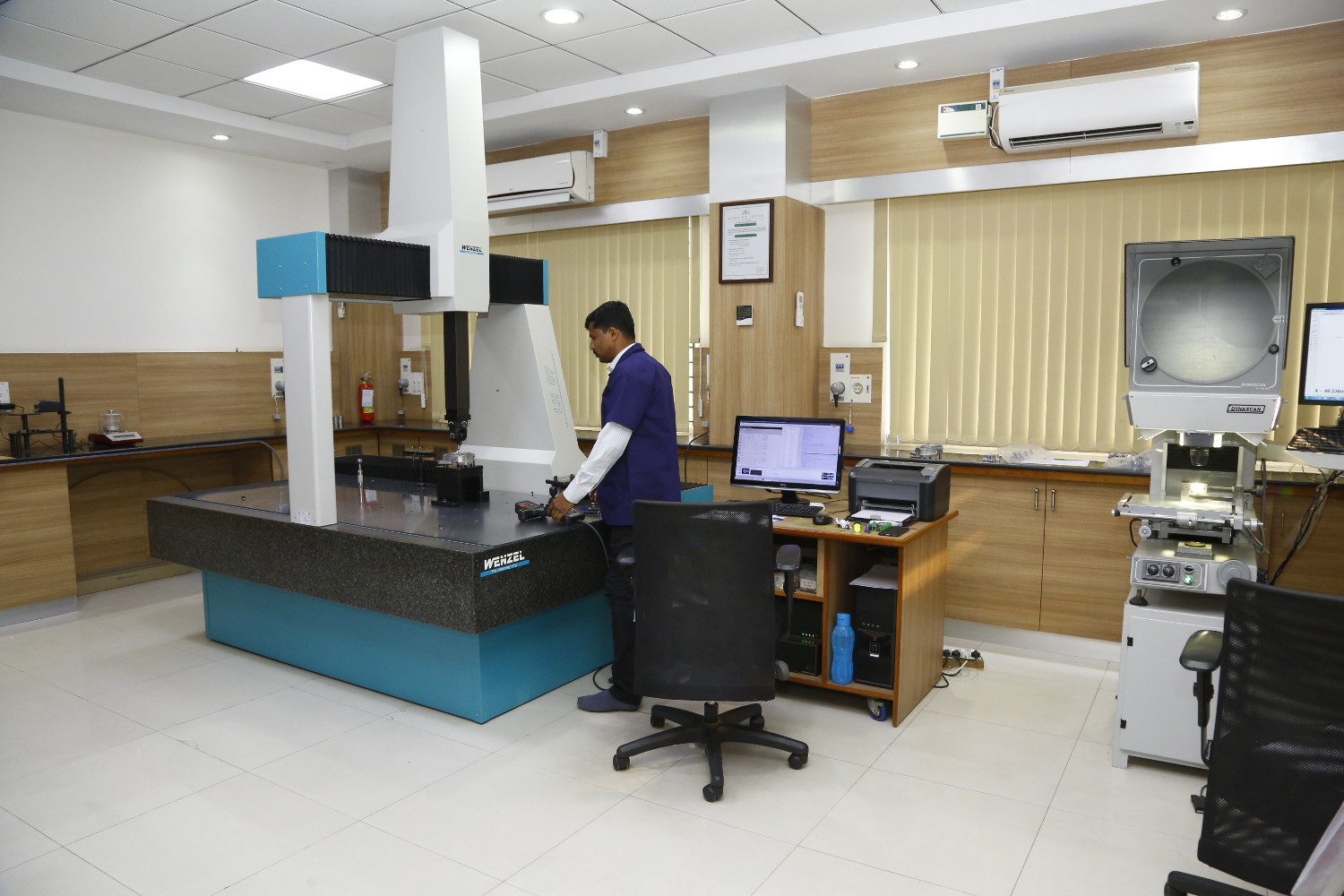
Metrology
At Alubee, the advanced state of art metrology department takes care of the dimensional verification activities for setting parts and all the development components. They are tested to ensure the accuracy, reliability, and precision of these components. The metrology lab follows the standards that are required by the customers and also the statutory norms required by the registered authorities for testing and verification.

Fettling – Post-casting Process
Once castings are produced, they are moved to the fettling process. Fettling is a post-casting operation. This post-casting operation includes linishing, trimming, filing, shot blasting, and Vibro finishing. After the gates are linished, the components are moved for the trimming operation. After trimming, the minor burrs are removed manually and sent to shot blasting operations. Based on the customer and the process requirement, either shot blasting or Vibro or both of these operations are carried out.
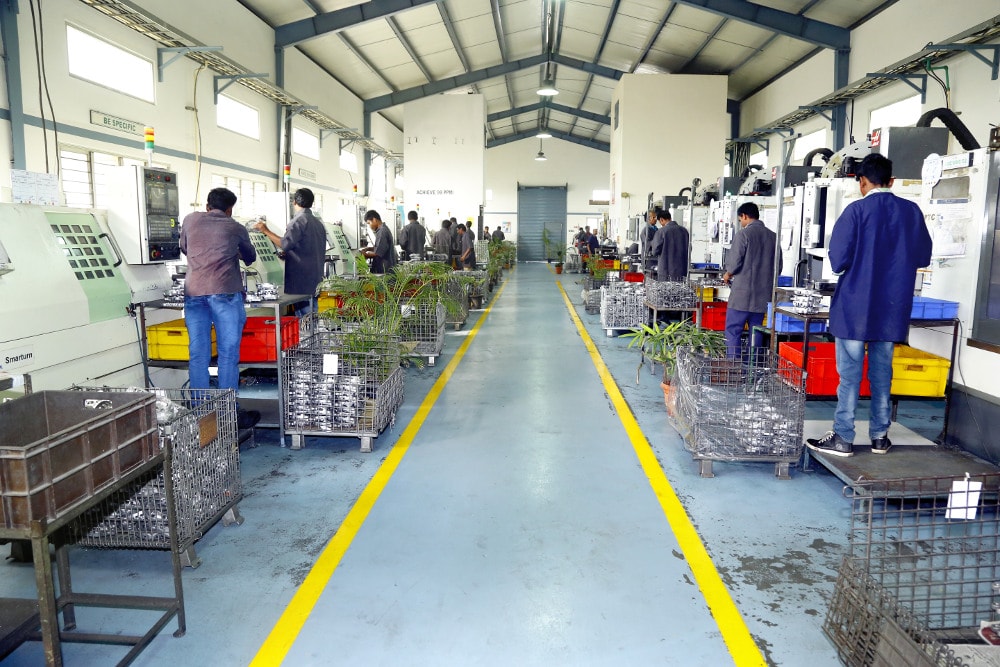
CNC / VMC Machining
The performance of any product majorly depends on the dimensional accuracy of the components. The accuracy of the components further depends on the accuracy of the machining process. Computerized numerically controlled machining centers and vertical milling machining centers help Alubee to produce high precision components.
Alubee has a state-of-the-art CNC machine shop, which consists of CNC machines and VMC machines. The HASS model VMC centers are imported from the United States and ensure high accuracy and productivity. The consistency and repeatability of these machines are excellent. LMW CNC lathes ensure the customer requirements are met 100%.
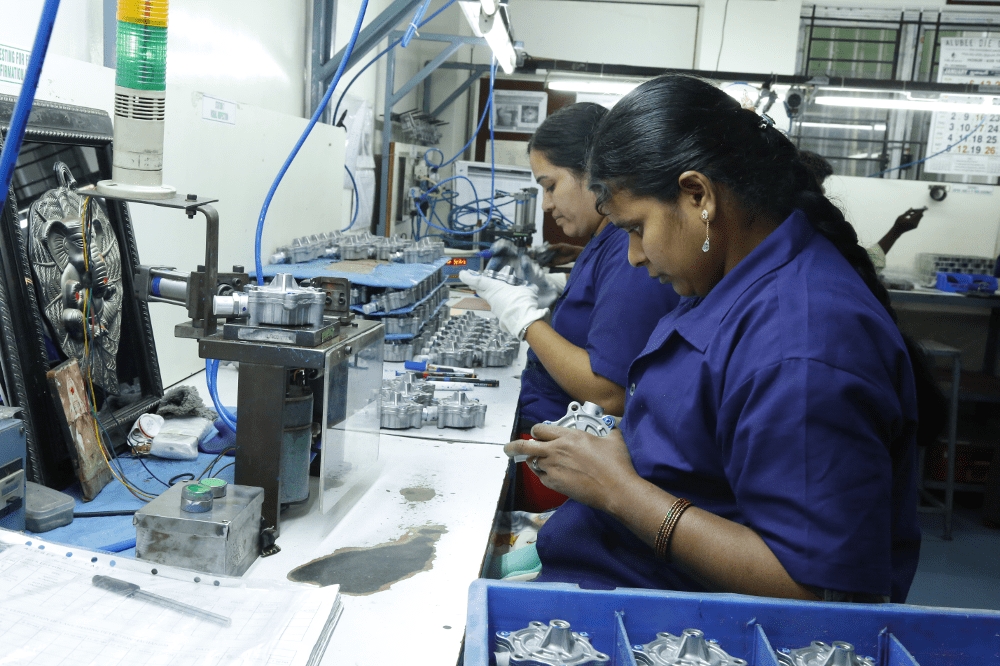
Assembly
The vacuum pump assembly is one of the challenging assignments Alubee has undertaken. Safety is a prime factor since the component is part of the brake assembly system. The vacuum pump assembly consists of the pump housing, pump plat, the rotor, and the O-ring. The electronic leak tester ensures the pump does not have any leak. The auto-confirmation mark after the assembly ensures that the leak is appropriately tested and passed. Alubee has the capacity of assembling around 2000 assemblies per shift.
GET IN TOUCH
Alubee Die Casters, Plot #20, A, SIPCOT – Phase 1, Hosur – 635126, Krishnagiri Dist, Tamilnadu